Exploring the Importance of GRP Enclosure Manufacturers
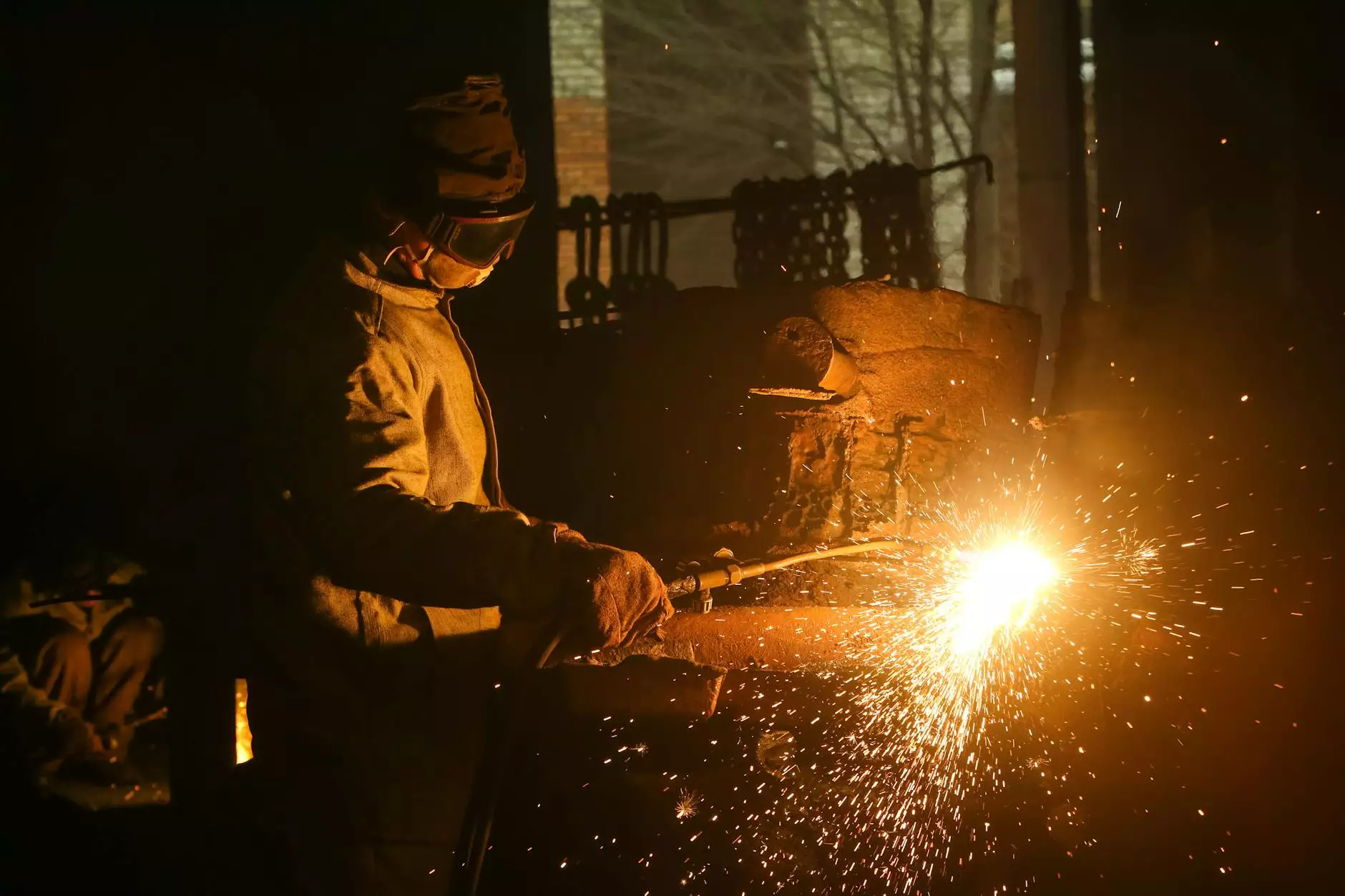
In today's rapidly evolving industrial landscape, the role of GRP enclosure manufacturers has become increasingly significant. Glass Reinforced Plastic (GRP) enclosures offer a unique combination of durability, weather resistance, and lightweight properties that are essential in numerous applications. This article delves into the extensive benefits, applications, and manufacturing processes associated with GRP enclosures, emphasizing why they are the preferred choice across diverse sectors.
What are GRP Enclosures?
GRP enclosures, often referred to as fiberglass enclosures, are protective casings made from composite materials primarily consisting of glass fibers and resin. The manufacturing process involves a technique known as fiberglass reinforcement, wherein glass fibers are combined with a resin matrix to create a robust structure. These enclosures are designed to house sensitive equipment, instrumentation, and various types of electrical apparatus, providing a safe and durable environment.
Key Advantages of GRP Enclosures
The growing popularity of GRP enclosures can be attributed to their multitude of advantages:
- Corrosion Resistance: Unlike traditional materials such as metal, GRP does not corrode, making it ideal for use in harsh environments.
- Lightweight: GRP enclosures are significantly lighter than metal counterparts, which simplifies transportation and installation.
- Thermal Insulation: These enclosures provide excellent thermal insulation, protecting sensitive equipment from temperature extremes.
- Customizability: GRP enclosures can be tailored to fit specific needs, offering various sizes, shapes, and colors.
- Low Maintenance: The durability of GRP translates to less frequent maintenance and lower long-term costs.
- Electrical Insulation: Glass-reinforced panels are non-conductive, enhancing safety for electrical applications.
Applications of GRP Enclosures
The versatility of GRP enclosures allows them to be utilized in a wide array of industries:
1. Telecommunications
Telecommunications infrastructure often requires robust and durable enclosures to protect sensitive equipment from environmental stressors. GRP enclosures serve as ideal solutions for housing telecommunications gear, ensuring reliable operation under diverse weather conditions.
2. Transportation
In the transportation sector, GRP enclosures are used for various applications, including train and bus shelters, as well as for housing signaling and control equipment. Their lightweight nature significantly simplifies installation while ensuring protection from vandalism and environmental damage.
3. Energy Sector
Both renewable and non-renewable energy sectors utilize GRP enclosures to protect control panels, electrical connections, and other critical equipment against harsh conditions, such as wind, rain, and high humidity.
4. Water and Waste Management
GRP enclosures are extensively used in water treatment plants and waste management facilities to safeguard sensitive instrumentation. Their corrosion-resistant nature makes them suitable for environments with exposure to chemicals and moisture.
5. Industrial Applications
From power distribution to manufacturing environments, GRP enclosures provide an essential layer of protection for machinery, control systems, and electrical components, enhancing operational efficiency and safety.
The Manufacturing Process of GRP Enclosures
Understanding how GRP enclosures are manufactured provides insights into their quality and performance. The process generally involves the following steps:
1. Material Selection
The first step in producing GRP enclosures is choosing high-quality raw materials. This includes the selection of glass fibers, resin types, and any additional materials necessary for reinforcement and finishing.
2. Molding
Once materials are selected, the next step is to create the mold. Various molding techniques, such as hand lay-up, spray-up, or injection molding, can be used depending on the desired strength and finish of the enclosure. Each technique has its advantages when it comes to production scale and material efficiency.
3. Layering
In the layering process, glass fibers are arranged and saturated with resin to form a solid structure. This is crucial for ensuring the enclosure’s strength and durability. Multiple layers are often applied to enhance structural integrity.
4. Curing
The next crucial phase is curing, where the resin hardens to form a solid piece. Curing can occur at room temperature or may require heat to accelerate the process, depending on the resins used.
5. Finishing
After curing, the GRP enclosure undergoes various finishing processes, including trimming, sanding, and painting, to achieve the required aesthetic and functional attributes.
Choosing the Right GRP Enclosure Manufacturer
When selecting a GRP enclosure manufacturer, several factors should be considered to ensure high-quality products:
- Experience: Look for manufacturers with a proven track record and expertise in producing GRP enclosures across different industries.
- Quality Assurance: Choose a company that implements stringent quality control processes to guarantee the durability and reliability of their products.
- Customization Capabilities: Ensure the manufacturer offers customization options to meet your specific needs, from sizing to additional features.
- After-Sales Support: Evaluate the level of support provided post-purchase, including warranty, maintenance, and customer service.
- Sustainability Practices: Investigate the manufacturer’s commitment to eco-friendly practices and materials, contributing to a sustainable future.
The Future of GRP Enclosures
The demand for GRP enclosures is expected to grow as industries increasingly prioritize safety, durability, and cost-effectiveness. Advancements in material science and manufacturing technologies are likely to foster innovations in GRP products, resulting in even more efficient and sustainable solutions. Furthermore, with rising concerns regarding environmental impact, the shift towards using recyclable materials in composite manufacturing will contribute to a greener future for GRP enclosures.
Conclusion
In conclusion, GRP enclosure manufacturers play a pivotal role in providing robust solutions that meet the needs of various industries. The combination of versatility, durability, and cost-effectiveness positions GRP enclosures as a leading choice for housing critical equipment. As technology evolves and industries embrace sustainable practices, the future of GRP enclosures is bright, with exciting possibilities awaiting. Understanding the benefits and capabilities of these enclosures can empower businesses to make informed decisions that enhance both safety and operational efficiency.
For high-quality, customizable GRP enclosures, Celtic Composites is your trusted partner, offering innovative solutions tailored to your specifications.