PSSR Inspection in South Wales: Understanding Its Importance for Your Business
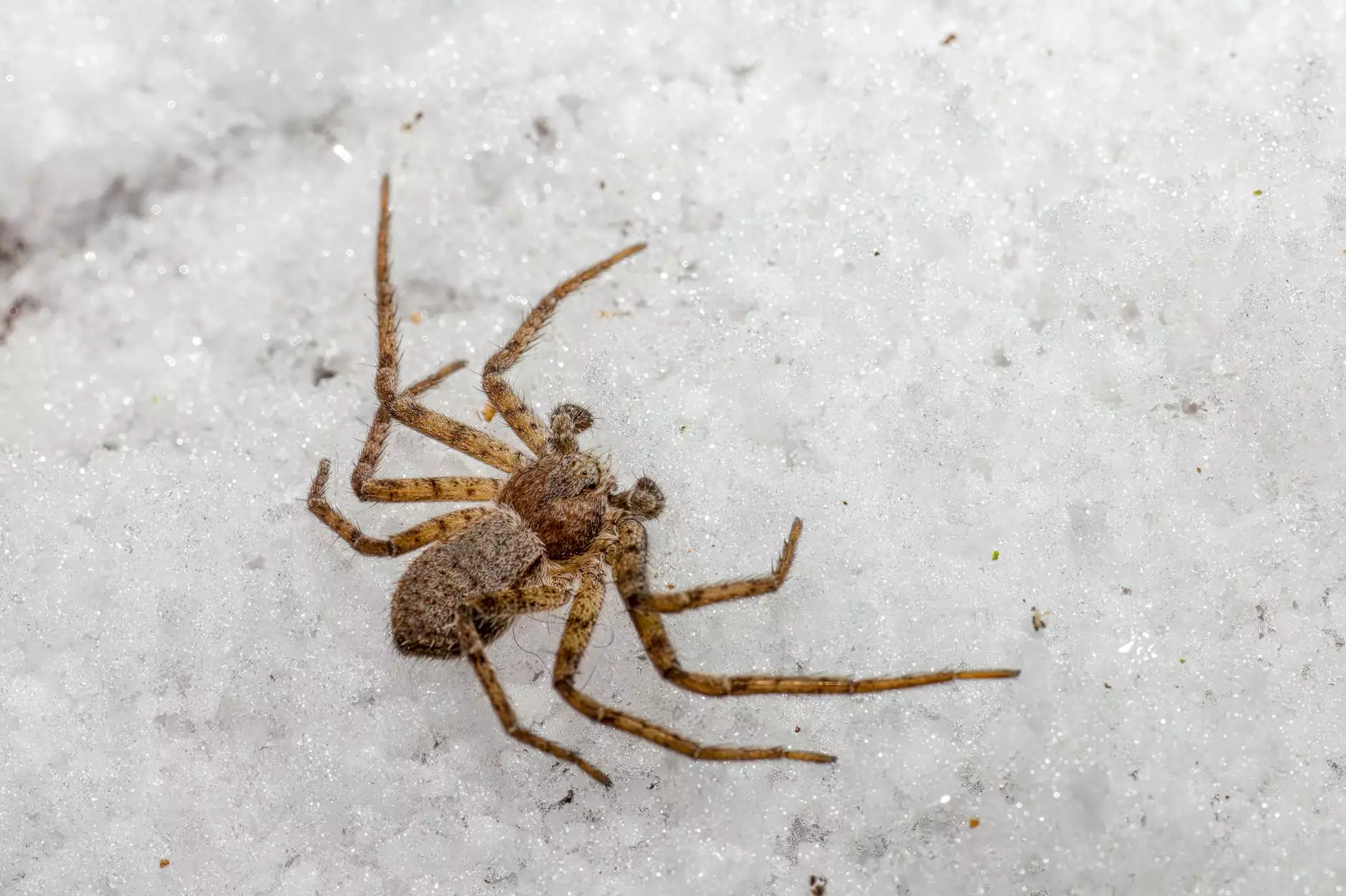
Process Safety and Safety Regulations (PSSR) inspections are critical for any business that utilizes pressure systems. In South Wales, these inspections ensure that conditions adhere to legal safety requirements while also promoting safe operating environments. This article is a comprehensive guide dedicated to exploring PSSR inspections, offering insights into their significance, processes, and benefits for businesses in South Wales.
What is PSSR Inspection?
The Pressure Systems Safety Regulations (PSSR) were established in the UK to ensure that systems operating under pressure are managed safely, effectively preventing accidents and equipment failures. This regulation primarily applies to pressure systems involving:
- Boilers
- Pressure vessels
- Pipes
- Heat exchangers
- Steam systems
As pressure systems can be hazardous, the PSSR inspection process involves a thorough examination to ascertain that these systems are adequately designed, installed, and maintained.
Why is PSSR Inspection Important for Businesses in South Wales?
Understanding the importance of PSSR inspection is crucial for any business operating in South Wales. Here are several compelling reasons:
- Regulatory Compliance: Adhering to PSSR is not just for safety; it's a legal requirement. Failure to comply can lead to severe penalties, including fines and legal repercussions.
- Accident Prevention: Regular inspections can identify potential hazards before they result in significant issues, protecting employees, equipment, and the environment.
- Enhanced Safety Culture: Implementing regular PSSR inspections fosters a culture of safety within your organization, emphasizing the importance of safety to your team.
- Operational Efficiency: Well-maintained pressure systems operate more efficiently, which can lead to cost savings and increased productivity.
How Often Should PSSR Inspections be Conducted?
According to industry standards, PSSR inspections should typically be carried out at least every 12 months, although this frequency can vary based on the specific equipment and its usage. For safety-critical systems or where changes occur in operation, more frequent inspections may be necessary.
Determining Inspection Frequency
To determine the frequency of PSSR inspections, consider the following factors:
- Age and condition of the pressure equipment
- Category and risk of activities being conducted
- Changes in operational practices
- Any previous incidents or failures
PSSR Inspection Process Explained
The PSSR inspection process typically involves several key steps to ensure a complete and thorough examination:
1. Initial Assessment
An initial assessment focuses on understanding your pressure equipment and its operating conditions. It is crucial to compile all operating documents and maintenance records, which will aid the inspector in evaluating the system's history and current practices.
2. Visual Inspection
During the visual inspection, the inspector will examine the equipment for obvious signs of wear, damage, or corrosion. This step is significant as it helps in identifying immediate hazards.
3. Functional Testing
Functional tests may include pressure testing and performance evaluations to ensure that all safety devices operate correctly. This simulation under real conditions helps establish reliability.
4. Documentation and Reporting
After the inspection, a report detailing the findings, recommendations, and any required actions is compiled. This documentation is essential for compliance and future reference.
Choosing the Right PSSR Inspection Provider in South Wales
Selecting a competent inspection provider is fundamental for effective PSSR compliance. Here are some tips for making an informed choice:
- Certification and Experience: Ensure that the inspectors are certified and have a solid track record in performing PSSR inspections.
- Industry Reputation: Look for reviews and testimonials from previous clients to gauge reliability and expertise.
- Tailored Services: Choose a provider who can offer personalized solutions based on your business’s unique needs.
- Post-Inspection Support: A good provider will not only conduct the inspection but will also assist you in addressing any identified issues and compliance requirements.
Benefits of Regular PSSR Inspections
Engaging in regular PSSR inspections provides numerous benefits for businesses:
- Risk Mitigation: Identifying issues before they escalate ensures a safer work environment.
- Increased Lifespan: Regular maintenance and inspections prolong the lifespan of your pressure systems.
- Cost Savings: Preventative measures can save your business money by avoiding costly downtime or repairs.
- Enhanced Employee Confidence: A commitment to safety builds confidence among employees, fostering higher morale and productivity.
Conclusion
In conclusion, PSSR inspection in South Wales is not merely a regulatory formality but an essential practice that safeguards your business, your employees, and the community. By embracing the PSSR framework and ensuring regular inspections, you establish a robust safety culture that leads to operational excellence and resilience. Choose a reliable inspection provider, stay compliant, and propel your business forward with the peace of mind that comes from knowing your pressure systems are secure.
For more information and to schedule your PSSR inspection, visit safeplantuk.co.uk today.
pssr inspection south wales