Understanding ABS M30 Material: The Future of Design and 3D Printing
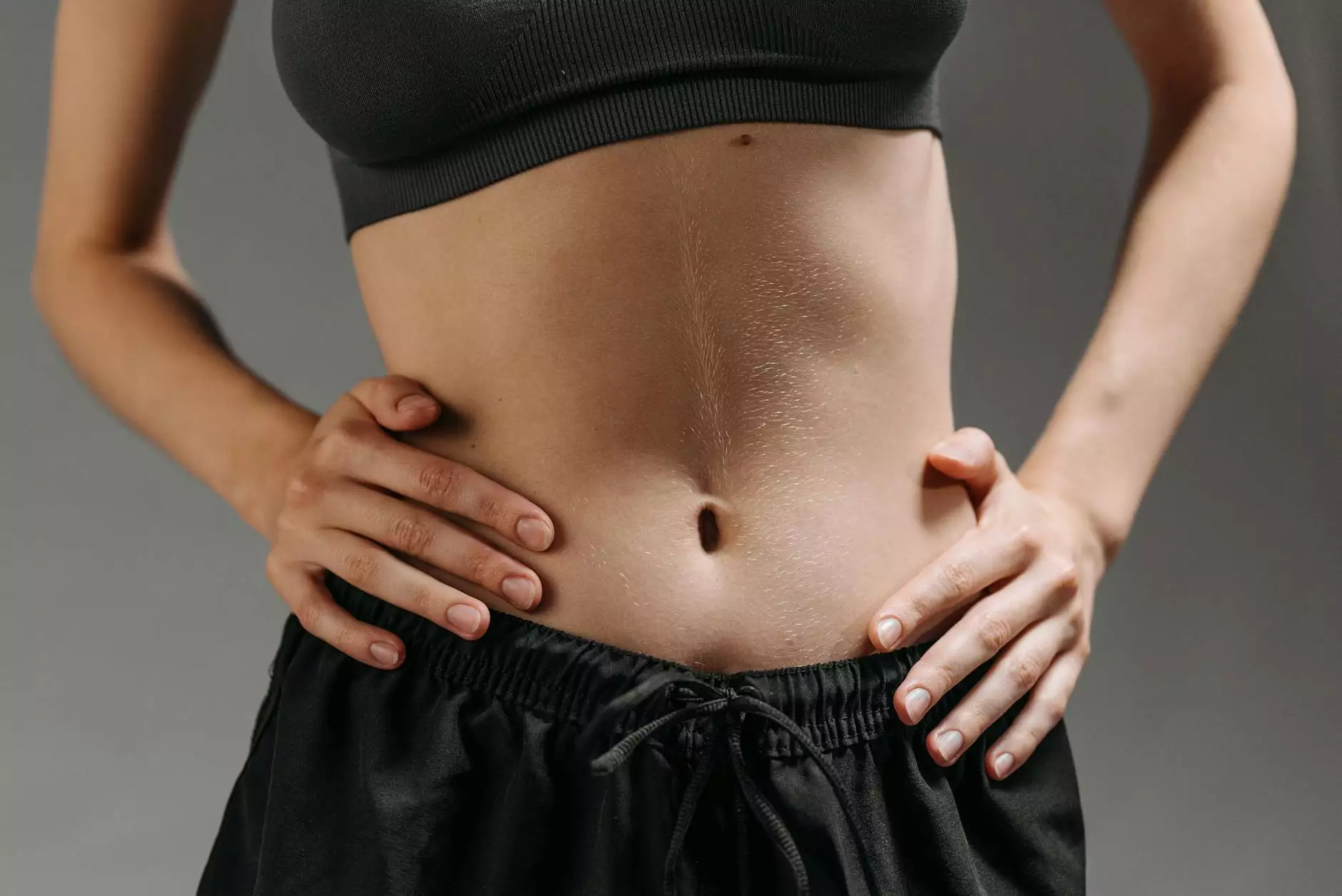
ABS M30 material is revolutionizing the fields of art supplies, product design, and 3D printing. Known for its excellent balance of strength, durability, and flexibility, this thermoplastic polymer is gaining traction among manufacturers and designers alike. In this article, we will delve into what ABS M30 is, its properties, advantages, and the various applications that make it a preferred choice for many industries.
What is ABS M30 Material?
ABS, or Acrylonitrile Butadiene Styrene, is a widely used thermoplastic known for its robustness and versatility. The designation "M30" typically refers to a specific grade or formulation of ABS, optimized for particular applications that demand higher impact resistance and improved mechanical properties.
The Chemical Composition of ABS M30
Understanding the chemical composition of ABS is essential to appreciate its capabilities. ABS is a copolymer made from three monomers: acrylonitrile, butadiene, and styrene. The combination of these materials results in a polymer that boasts:
- High Impact Resistance: The butadiene component provides flexibility, while styrene adds structural integrity.
- Thermal Stability: ABS M30 can withstand higher temperatures than standard ABS, making it ideal for more demanding applications.
- Excellent Adhesion: This material adheres well to various coatings and finishes, enhancing aesthetic appeal.
Properties of ABS M30 Material
When it comes to material selection for product design, the properties of ABS M30 are of utmost importance. Let’s explore some of its key attributes:
- Durability: ABS M30 is designed to endure stress and impact, making it suitable for products exposed to wear and tear.
- Flexibility: It maintains a certain level of bendability without cracking, which is essential for dynamic designs.
- Easy to Machine: Compared to other thermoplastics, ABS M30 can be easily molded and processed, allowing for innovative designs.
- Low Density: The lightweight nature of ABS M30 makes it a popular choice for applications where weight savings are crucial.
- Color Versatility: ABS M30 can be produced in various colors, allowing for creative freedom in design.
Advantages of Using ABS M30 Material
With its superior qualities, it's no wonder that ABS M30 is becoming a favorite in various industries:
- Cost-Effective: The production process of ABS is relatively inexpensive, providing a cost-effective solution for manufacturers.
- Sustainability: ABS can be recycled, reducing its impact on the environment.
- Wide Application Range: From toys to automotive parts, the versatility of ABS M30 knows no bounds.
- Compatibility with 3D Printing: Its thermal properties make ABS M30 an ideal material for various 3D printing technologies, enhancing the capabilities of this emerging industry.
Applications of ABS M30 Material
Due to its properties and advantages, ABS M30 material can be found in a myriad of applications, especially in art supplies, product design, and 3D printing:
In Art Supplies
ABS M30 material is used in the production of art supplies that require durability and colorfastness. Items such as:
- Artistic tools like rulers and templates.
- Durable figurines and models for educational purposes.
- Various packaging applications for art materials.
In Product Design
Product designers rely heavily on ABS M30 for creating stylish and functional prototypes. Its strength-to-weight ratio makes it ideal for:
- Housing for electronic devices.
- Consumer product prototypes.
- User interface elements in automotive design.
In 3D Printing
As 3D printing continues to evolve, ABS M30 material is becoming a go-to choice for many makers. It is used in:
- 3D printed parts that require strength and flexibility.
- Functional prototypes that must withstand operational stress.
- Artistic sculptures and custom designs with intricate details.
Comparison with Other Materials
When considering materials for design and manufacturing, it’s crucial to understand how ABS M30 compares to other thermoplastics:
ABS M30 vs. PLA
PLA (Polylactic Acid) is often preferred for its ease of printing and biodegradable properties. However, ABS M30 is superior in:
- Durability: ABS M30 offers greater resistance to impacts.
- Heat Resistance: ABS M30 can withstand higher temperatures without losing structural integrity.
ABS M30 vs. Nylon
Nylon is another strong contender in the thermoplastic realm. However, it may not be as easy to print as ABS M30. Key differences include:
- Cost: ABS M30 is generally more cost-effective than Nylon.
- Ease of Use: ABS M30 is easier to work with in various applications compared to Nylon.
Best Practices for Working with ABS M30 Material
To maximize the benefits of ABS M30, here are some best practices for handling this material:
- Temperature Control: Maintain appropriate heat settings during processing to avoid warping.
- Cooling Rate: Ensure gradual cooling to prevent stress cracks.
- Ventilation: Ensure adequate ventilation while 3D printing as ABS can emit fumes that may be harmful.
The Future of ABS M30 Material
The future looks bright for the use of ABS M30 in various industries. As technology advances, researchers are exploring new formulations that enhance its properties further. The potential for combining ABS M30 with other materials, creating composites, and new manufacturing techniques means that this material will continue to be a staple in both product development and artistic applications.
Conclusion
In conclusion, ABS M30 material stands out as a leading choice for anyone involved in art supplies, product design, and 3D printing. Its unique blend of durability, flexibility, and cost-effectiveness makes it an undeniable asset in both traditional crafting and modern manufacturing techniques. As industries continue to innovate and expand, the use of ABS M30 material is set to thrive, offering endless possibilities for creative minds and engineers alike.
For more information on quality materials like ABS M30 and their applications, visit arti90.com.