Understanding the Significance of Plastic Injection Tooling in Manufacturing
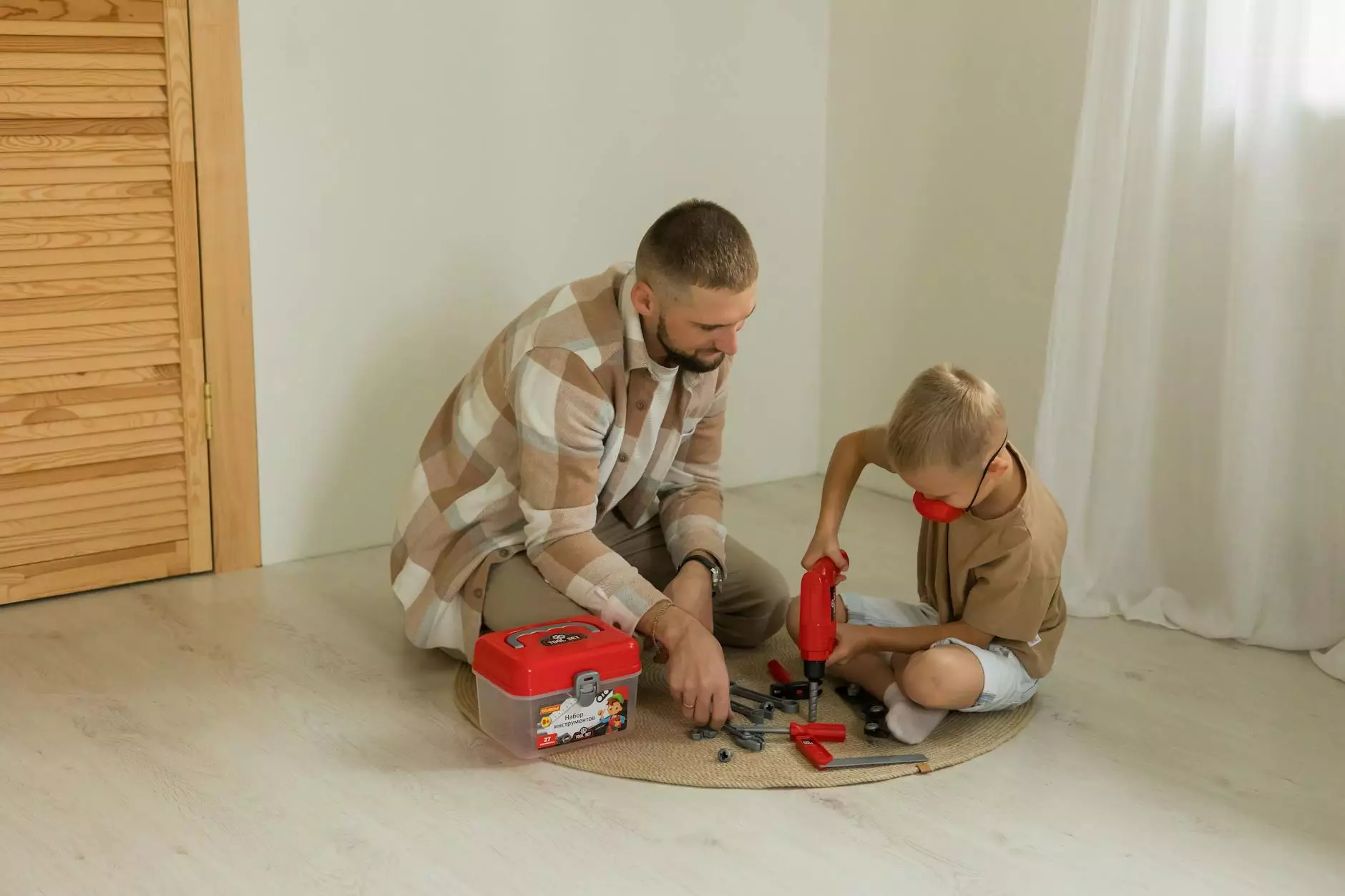
In today's competitive manufacturing landscape, efficient processes and precision engineering are paramount. One of the pivotal techniques that has emerged is plastic injection tooling. This process not only allows for high-volume production but also ensures that products maintain a level of quality and consistency that is essential in various applications. In this article, we delve into plastic injection tooling and explore its critical role in the realm of manufacturing, particularly for metal fabricators.
What is Plastic Injection Tooling?
Plastic injection tooling is a manufacturing process that involves the creation of parts by injecting molten plastic into a mold. The mold is generally made of high-quality steel or aluminum, which allows it to withstand high pressures during the injection process. Once the plastic cools and solidifies, the mold opens, and the finished part is ejected.
The Advantages of Plastic Injection Tooling
Plastic injection tooling offers a myriad of benefits to manufacturers, especially to those in the field of metal fabrication. Here are some of the most significant advantages:
- Cost Efficiency: Once the initial mold is created, the cost per part decreases significantly, making it ideal for large production volumes.
- High Precision: This process offers exceptional precision, ensuring that each product is manufactured to exact specifications, thus reducing waste.
- Versatility: Plastic injection molding can accommodate a wide range of thermoplastics and thermoset materials, providing flexibility in design.
- Complex Designs: The technology allows for intricate designs and complex geometries that would be difficult or impossible to achieve with other methods.
- Fast Production Times: The speed of production in plastic injection molding is unmatched by many other manufacturing processes, facilitating quicker market entry.
The Process of Plastic Injection Tooling
Understanding the workflow of plastic injection tooling is essential for grasping its efficacy. Here's a step-by-step breakdown of the process:
- Design Phase: The process starts with a detailed design of the component or product, often created using CAD (Computer-Aided Design) software.
- Mold Creation: After finalizing the design, a mold is created, which is custom-built to reflect the exact specifications of the desired output.
- Injection of Material: The selected plastic material is heated until it reaches a molten state, then injected into the mold under high pressure.
- Cooling: The molten plastic cools and solidifies within the mold, taking on the shape of the desired part.
- Ejection: Once cooled, the mold opens to release the finished part, which may undergo further finishing processes.
Applications of Plastic Injection Tooling
Plastic injection tooling finds its applications across a wide array of industries due to its versatility. Some key sectors include:
- Automotive: Used for creating interior and exterior components, such as dashboards, panels, and even housing for electronic devices.
- Consumer Goods: From toys to kitchen utensils, plastic injection moldings ensure durability and functionality.
- Medical Devices: Critical for producing syringes, surgical tools, and various disposable medical devices that require strict cleanliness standards.
- Electronics: Essential in manufacturing housings and components for various electronic devices.
- Industrial Equipment: Utilized to create parts for machinery and tools that benefit from light-weighting and precision.
Challenges in Plastic Injection Tooling
While plastic injection tooling offers substantial benefits, there are also challenges that manufacturers must be aware of:
- Initial Costs: The cost of designing and creating molds can be significant, which may deter smaller manufacturers.
- Material Limitations: Although many plastics can be used, some specific applications may require materials that don't perform well with injection molding.
- Complexity of Design: While it allows for complex designs, creating intricate molds can be technically challenging and requires expertise.
- Quality Control: Ensuring quality across large batches demands strict quality control measures to avoid defects.
Future Trends in Plastic Injection Tooling
The future of plastic injection tooling is set to evolve with advancements in technology and shifts in market demands. Potential trends include:
- Automation: The integration of robotics and AI in the manufacturing process to streamline operations and reduce human errors.
- 3D Printing: Combining both 3D printing and injection molding to allow for faster prototyping and production of complex shapes.
- Sustainable Materials: Increasing use of biodegradable and recycled plastics that align with environmental goals.
- Smart Manufacturing: The adoption of IoT technology for real-time monitoring and optimization of the injection molding process.
Why Choose DeepMould for Plastic Injection Tooling?
For businesses looking to implement plastic injection tooling, choosing the right partner is crucial. DeepMould stands out as a premier destination for all your injection mold needs. Here’s why:
- Expertise: With years of experience in the industry, our team possesses the knowledge required to tackle complex projects efficiently.
- Quality Assurance: We maintain rigorous quality control protocols to ensure that every component meets the highest standards.
- Customized Solutions: Our ability to provide tailored solutions means we can accommodate unique customer specifications and requirements.
- State-of-the-Art Technology: We leverage the latest in manufacturing technology to improve efficiency and production outcomes.
- Customer Support: Our commitment to customer satisfaction is reflected in our responsive support and collaboration throughout the project lifecycle.
Conclusion
In conclusion, plastic injection tooling is an indispensable process in the modern manufacturing landscape, offering numerous advantages from cost savings to design flexibility. For metal fabricators and other manufacturers seeking to enhance their production capabilities, understanding and utilizing this technology is key. With the potential for future advancements and continuous improvement, the role of plastic injection tooling is only set to grow, making it essential for businesses looking to forge ahead in a competitive market.
Explore how your business can benefit from the precision and efficiency of plastic injection tooling today. Connect with us at DeepMould, and let’s take your manufacturing processes to new heights.